一、班组简介
北京北方车辆集团有限公司工具液压分厂攻坚班成立于2010年,主要承担履带装甲车辆液压、联接、传操等关键零部件的制造加工,共有员工29人,其中高级技师4名、技师5名,具有大专以上学历的员工占比达80%。2016年班组实现收入845万元,全员劳产率29.15万元/人﹒年。2014年班组参与北京APEC会议特效焰火发射任务,受到会议筹备委员会“激动、震撼、世界第一”的高度评价;2015年参与93阅兵装备的制造和保障,获得总装备部颁发的装甲装备保障突出贡献奖。2015年班组获“全国质量信得过班组”,2016年获北京市“青年安全示范岗”。
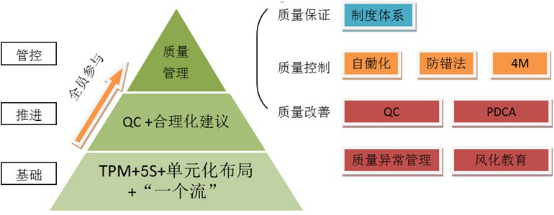
二、获奖概览
“54ATP”质量管理法
班组通过质量理念与精益方法的有效融合,逐渐形成了别具特色的“54ATP”(“5S、4M、自働化、合理化建议、TPM”)质量管理法。即在5S和TPM管理的基础上,大力推进“单元化布局+一个流”的改进优化工作,采取加工流程再造、自働化、工具互用、一人多机等措施,以产品族划分,组建6个各具特色的生产单元,并逐步形成全过程覆盖的质量管控手段(标准作业、防错、4M),全员参与的质量持续改善风尚(QC、合理化建议),实现了班组精细化管理水平稳步提升。
三、质量管理经验
1.全员参与,推进基础提升
班组围绕5S 、TPM等精益管理基础工作,深耕细作,建立筑牢质量管理基础。现场以整理、整顿、清扫、清洁、素养及安全为抓手,实现了有物必有区、有区必分类、分类必到人的现场定制和责任归属管理,逐步形成了人人自觉维护现场环境、遵守现场规定的良好工作素养。此外,班组通过专业人员的专业保全和班组员工的自我保全、设备的日保和周保、设备保养流程和保养标准,使得设备故障率明显降低。
随着精益理念的深入人心和精益方法的不断实践,班组大力推进“单元化布局+一个流”的改进优化工作,采取加工流程再造、自働化改造、工具互用、一人多机等措施,组建了以“全国五一劳动奖章获得者马小光”、“兵器级劳动模范刘阳”命名的“马小光液压件U型加工单元”、“刘阳联接件自动加工单元”等6个生产单元,实现了工序作业紧密衔接,产品流畅周转,以及生产调度快速响应,推动班组精细化管理水平稳步提升。
刘阳联接件自动加工单元对内六角螺栓开展了质量效率提升联合攻关。该产品体积小、基数大,按原工艺,零件加工需6名工人、6台设备,占用生产资源较多,生产效率低下,且产品质量不稳定。
围绕以上问题,进行基础提升改进:
(1)调整单元布局:配备立式钻床,车床与钻床相邻放置,减少车、钻工序间的物流距离;人员配置以一人多机为基础,减少加工过程中的等待浪费。
(2)革新工艺:采用全功能数控车,将原有的10道工序合并为2道,一次装夹完成所有工序加工,背面倒角在钻床完成。减少工序流转,优化工序顺序,固化数控程序、刀具种类、规格等。
(3)改造设备:对原有设备进行设计改造,实现了自动上料、自动装夹校正、优化加工程序,一次装夹成型,并通过机械抓手自动下料,减少了上下料的辅助时间和工序间的周转等待时间,实现了全自动化的加工流程,保证了产品的加工一致性,提高了生产效率和质量。
(4)管理刀具寿命:钻孔工作量占到整体工作量的40%-50%,采用硬质合金刀具,性能超出高速钢刀具30-50%,刃磨次数明显减少,转速及进给数值相应提升,生产效率显著提高。
2.制度约束,持续推进改善
通过全员参与QC小组活动、合理化建议活动等,持续改进、不断丰富完善加工单元的基础能力。并以此为基础,夯实提高质量管理能力,齐头并进抓好质量保证、质量控制、质量改善三大工作板块,建立并完善了一整套质量管理办法。
(1)质量保证
班组定期组织员工学习公司质量体系文件及分厂的《质量控制及考核管理办法》、《每日质量巡检规范》、《班前会管理规范》等规章制度,细化员工每日行为规范,如作业标准、控制要点等,指导员工掌握质量改善方法,如PDCA循环,QC小组活动等。
(2)质量控制
为进行有效的质量控制,班组必须做好 “防止质量问题发生”和“避免质量问题传递”两项工作。
班组对各项产品实施严格的质量控制规定,加强对产品入库、贮存、转运管理,设计了通用料架和转运工装,确保不挤压、不磕碰。
在生产过程中,班组对4M变化点实施有效的记录和管控,并严格执行班组“三个首检”,即交接班后首检,刀具更换后首检,设备启动后首检,使各变化点处于受控状态,实现平稳作业,确保产品质量,预防产生不合格品。
(3)质量改善
针对工作中发现的质量异常,按照流程倒排、重点分析、举一反三的工作方法,理清技术和管理上漏洞,形成问题闭环管理,并进行专题教育。通过开展QC活动,以问题为导向,以生产需要为出发点,以技术、管理的短板为突破口,大胆尝试、积极改善,不断总结提高。班组全年累计提出合理化建议97条,采纳率91.8%,员工参与率82.8%,注册的QC课题“提高内六角螺栓生产效率”获“中国兵器行业QC成果二等奖”。
近年来,班组不断结合全价值链体系化精益管理战略,将现场管理、产品质量控制作为班组管理的重点,开展“质量月”活动,并结合现场管理、5S、精益生产、合理化建议等活动,互相促进,切实有效的提高了产品的质量和运营效率。